How Do You Ensure The Quality Of custom product packaging?
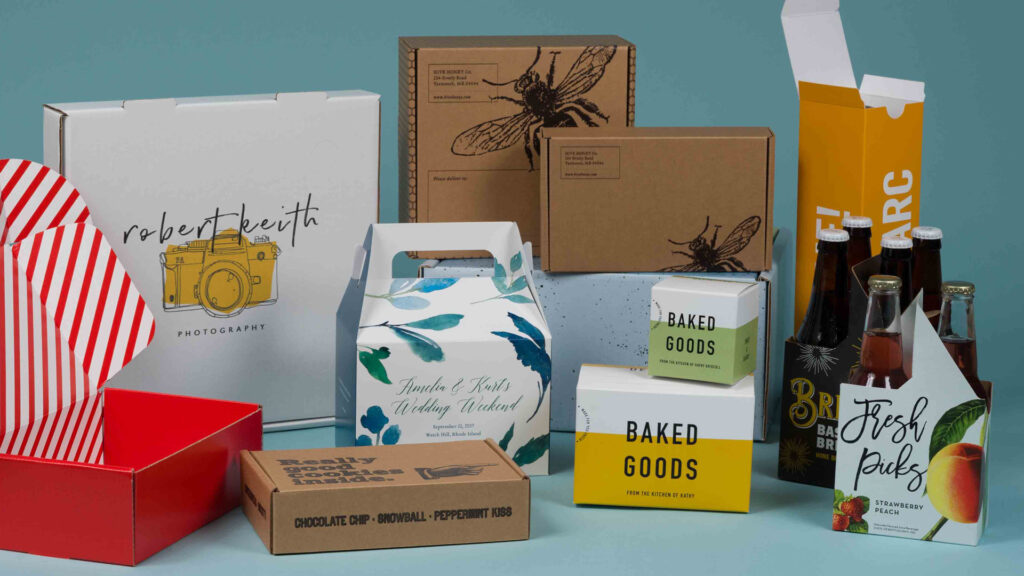
custom product packaging
Custom product packaging are more than just a container; they’re a critical aspect of a product’s presentation and protection. Ensuring the quality of these boxes is essential for maintaining brand reputation, safeguarding the product, and delivering a positive consumer experience. In this article, we’ll explore how to ensure the quality of custom product packaging through various stages, from material selection to final manufacturing.
Key Factors for Ensuring Quality
Choosing the Right Material
The first step in ensuring the quality of custom product packaging is selecting the appropriate material. The choice of material—whether it’s corrugated cardboard, paperboard, or specialty materials—depends on the product’s requirements and intended use. High-quality materials offer durability, protection, and a premium feel that reflects the brand’s commitment to quality.
Testing Material Durability
Once the material is selected, it’s crucial to test its durability. Conducting tests such as compression, puncture, and tear resistance ensures that the material can withstand the rigors of shipping, handling, and storage. Testing helps identify potential weaknesses and allows for adjustments before full-scale production.
Environmental Impact
Considering the environmental impact of packaging materials is increasingly important. Opt for materials that are recyclable, biodegradable, or made from sustainable sources. This not only aligns with eco-friendly practices but also appeals to environmentally-conscious consumers.
Design and Printing
Accurate Design Specifications
Design accuracy is vital for the quality of custom product packaging. Ensure that design specifications, such as dimensions, cut lines, and fold lines, are precise and align with the manufacturer’s capabilities. Accurate designs prevent production issues and ensure that the final product meets expectations.
Quality Printing Techniques
The printing process significantly affects the appearance and quality of custom boxes. Utilize high-quality printing techniques such as offset or digital printing to achieve sharp, vibrant images and text. Ensuring proper ink adhesion and avoiding smudging or fading are key to a professional finish.
Color Accuracy
Color consistency is crucial for maintaining brand integrity. Use color management systems and conduct print proofs to verify that the colors on the box match the intended design. Accurate color reproduction enhances the overall visual appeal and ensures brand recognition.
Manufacturing Process
Choosing a Reputable Manufacturer
Partner with a reputable manufacturer known for high-quality production standards. Research potential manufacturers, read reviews, and request samples to evaluate their work. A reliable manufacturer will adhere to quality standards and provide consistent results.
Quality Control Measures
Implement quality control measures throughout the manufacturing process. This includes regular inspections, testing of samples, and adherence to production guidelines. Quality control helps identify and address any issues before the final product reaches the consumer.
Consistency and Precision
Consistency in production is essential for maintaining quality across all custom product packaging. Ensure that the manufacturing process is precise, with consistent cutting, folding, and assembly. Variations in these processes can affect the overall quality and functionality of the boxes.
Prototype and Sampling
Creating Prototypes
Before full-scale production, create prototypes to evaluate the design, material, and functionality of the custom product packaging. Prototypes allow you to assess the overall look and feel of the box, make necessary adjustments, and ensure that it meets your quality standards.
Conducting Sample Tests
Sample testing involves evaluating a batch of custom boxes to verify their quality. Test the samples for durability, printing accuracy, and overall construction. Sample tests provide insights into potential issues and allow for adjustments before mass production.
Iterative Feedback and Adjustments
Use feedback from prototypes and samples to make iterative adjustments. This iterative process ensures that any issues are addressed early and that the final product meets the desired quality. Continuous feedback helps refine the design and production process.
Compliance and Standards
Industry Standards
Adhere to industry standards for packaging quality, including specifications for materials, design, and safety. Compliance with these standards ensures that the custom product packaging meet industry expectations and contribute to overall product quality.
Regulatory Compliance
Ensure that the packaging design complies with relevant regulations, such as labeling requirements and safety standards. Regulatory compliance is crucial for avoiding legal issues and ensuring that the product is safe for consumers.
Safety Requirements
Packaging should meet safety requirements to protect both the product and the consumer. This includes ensuring that the materials used are non-toxic, the packaging design is secure, and the product is safeguarded from tampering or contamination.
Conclusion
Ensuring the quality of custom product packaging involves careful attention to detail at every stage, from material selection and design to manufacturing and compliance. By choosing the right materials, implementing rigorous quality control measures, and adhering to industry standards, you can create custom boxes that enhance your product’s presentation, protect it during transit, and deliver a positive experience to consumers. A commitment to quality in packaging not only reflects well on your brand but also contributes to overall product success. For more insights and resources on custom product packaging, visit customproductpackaging.com.
FAQ’ s
What materials are best for custom product packaging?
Materials like corrugated cardboard, paperboard, and specialty materials are commonly used for custom product packaging. The choice depends on the product’s needs, such as durability, protection, and aesthetic appeal.
How do you ensure color accuracy in printing?
Color accuracy can be ensured by using color management systems, conducting print proofs, and verifying that the colors on the final product match the design specifications.
Why are prototypes important for quality assurance?
Prototypes allow you to evaluate the design, material, and functionality of the packaging before full-scale production. They help identify potential issues and make necessary adjustments to ensure quality.
What quality control measures should be taken during manufacturing?
Quality control measures include regular inspections, sample testing, adherence to production guidelines, and consistent manufacturing processes to ensure the final product meets quality standards.
How can I ensure compliance with packaging regulations?
Ensure that the packaging design adheres to relevant regulations, such as labeling requirements and safety standards. Regularly review and update packaging practices to maintain regulatory compliance.